3D printed houses bring the benefits of additive manufacturing to the construction space. The material costs incurred by construction 3D printing are usually an order of a magnitude less when compared to conventional methods. This is while we take into account the fact that 3D printing concrete tends to be more expensive than normal construction concrete.
As for labor costs, they drop down basically to the daily wages of at most two or three operators. And that too is for a much shorter length of time as the 3D printed house would be ready for finishing and furnishing in days instead of months.
The cost to build an average sized 3-bedroom house with conventional building methods is from $250,000 to $320,000. Building the same home with 3D printing technology would cost from 20 percent to 40 percent less to build. So that same 3-bedroom house would presumably cost between $140,000 to $240,000 to build with 3D printing technology.
It should be noted at this point, that most construction 3D printers will not build, or 3D print the foundations, nor would the construction 3D printer be of any cost-saving benefit when it comes to roofing the house.
All those things: the roof, the windows, the doors, electrical wiring, paint and finishing – all of these costs remain the same as with a conventional house, as all this fall outside the scope of what a construction 3D printer is capable of.
The cost of 3D printed house based on different builders
University of Nantes researchers designed and constructed a full-size single-family house via construction 3D printer in France at a cost of $232,000 in 2018. Which was twenty percent less than what a similar sized building would have cost to construct via conventional means.
Haus.me – the business that sells the PassivDom highly insulated prefabricated houses, charges $210,000 for a ready to move in luxury 3D printed smart house that is entirely self-sufficient and filled to the brim with smart features.
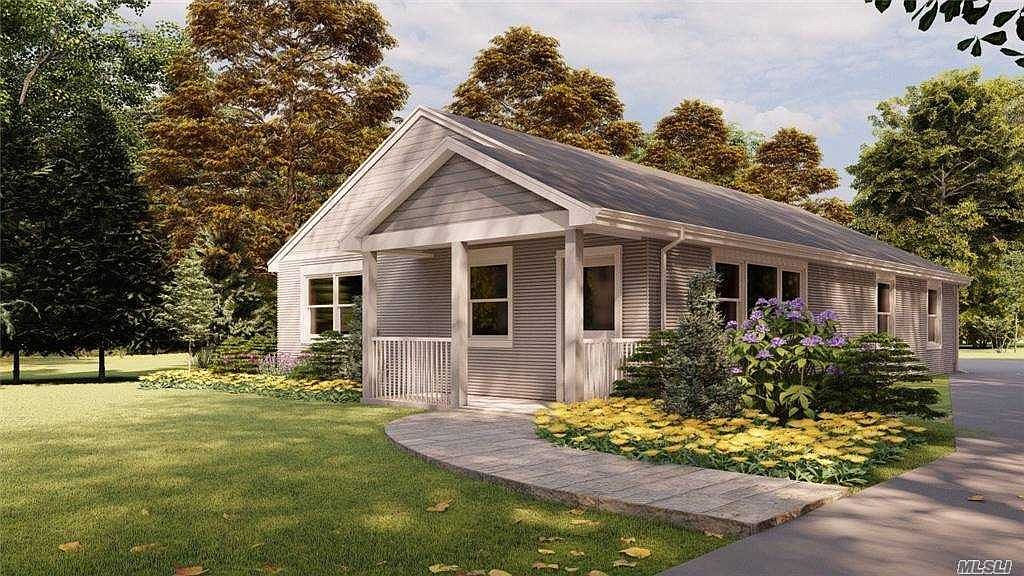
The Dubai Future Foundation office that was 3D printed off-site by Winsun cost $140,000 at the time for the entire structure. With the fit and finish of this luxury office, a hundred and forty thousand dollars is quite a bargain seeing as how by using construction 3D printing technology, the government estimates that it saved almost 50% on the total (assembly, electrical, and technical) labor costs.
All three of the above are examples of luxury or large-sized 3D printed houses that cost a sizably less amount than what an equivalent construction done via conventional methods would cost.
On the other end of the scale are the small size houses that have been making headlines and have successfully been 3D printed at a fraction of conventional costs.
COBOD’s construction 3D printing services provide an online project cost calculator based on various factors such as the square meter area of all the walls, labor cost and number of operators, and the cost per unit of 3D printing concrete.
The cost of construction comes out to be around $15,000 for a small sized house (single bedroom). $20,000-25,000 for a medium sized house (two bedroom). And around $50,000 for a large sized 4 bedrooms house.
Compare this with the fact that building one’s own house can cost anywhere between $95 to $150 per square foot and it quickly becomes clear that even construction 3D printing services have a lot to offer in terms of cost savings.
On the extreme end of affordable housing of course, stand ICON and WASP’s efforts.
ICON and New Story’s 500 sq. Foot houses 3D printed on-site in El Salvador cost around $4,000-5,000 per house.
And WASP’s earthen house village made with their construction 3D printer. The average raw material cost per house came out to only 48 euros per house.
Cost benefits in time savings offered by 3D printing a home
While costs are often the most quoted benefits of shifting to construction 3D printers. The time scale benefits are one of the most staggering numbers.
As a matter of fact, most 3D construction projects never need more than a month to 3D print even the most complex designs.
The Future Foundation Office of Dubai took a total of 3 months to go from idea to operational office.
Europe’s first 3D printed office, The BOD, only took 22 days on their first attempt, and this was reduced to just 3 days when COBOD reperformed the construction 3D printing of the building as a test 2 years later.
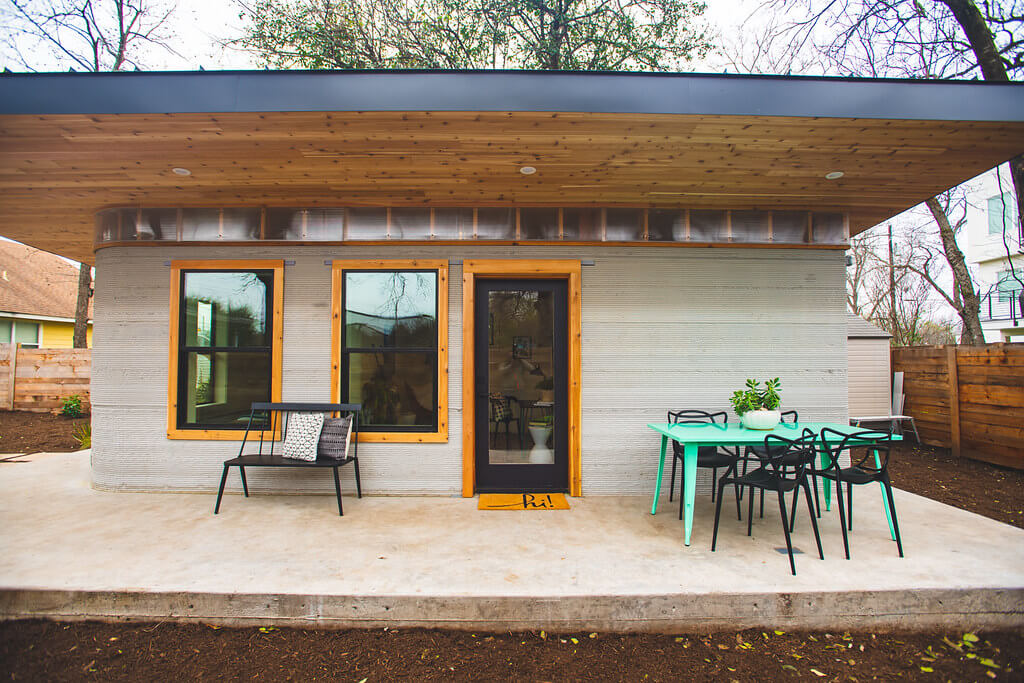
And of course, ICON’s 500 sq. foot houses take only a day each to go from nothing to a completely finished and ready-to-move-in house.
The mere thought of constructing an entire house in a single day is nothing short of amazing.
Compare this with conventional construction, and it is normal to expect ANY house to take at least several months to be ready to move in.
Where to buy 3D printed houses
As it stands, consumers in most cases would be unable to commission a 3D printed house construction directly. The printers themselves are expensive investments for any local construction company. 3D construction printer generally starts at $39,000 for the small basic models, to the upwards of $100,000 for the larger models.
Apart of from the cost of equipment and materials, there’s another major hurdle in purchasing a 3D printed house depending on where you are located. Only a handful of construction permit have been handed out for 3D printed houses, in special experimental cases, in select areas.
The mass of 3D printed houses is currently being developed in more technologically primitive areas. However, for anyone interested, a good place to start would be to contact the large-size local construction companies first. And then, as option B, contact the construction 3D printer makers themselves.
One exception of course, is Haus.me. The luxury prefabricated home maker readily sells its houses conveniently online via both monthly installments plans as well as outright cash purchases.
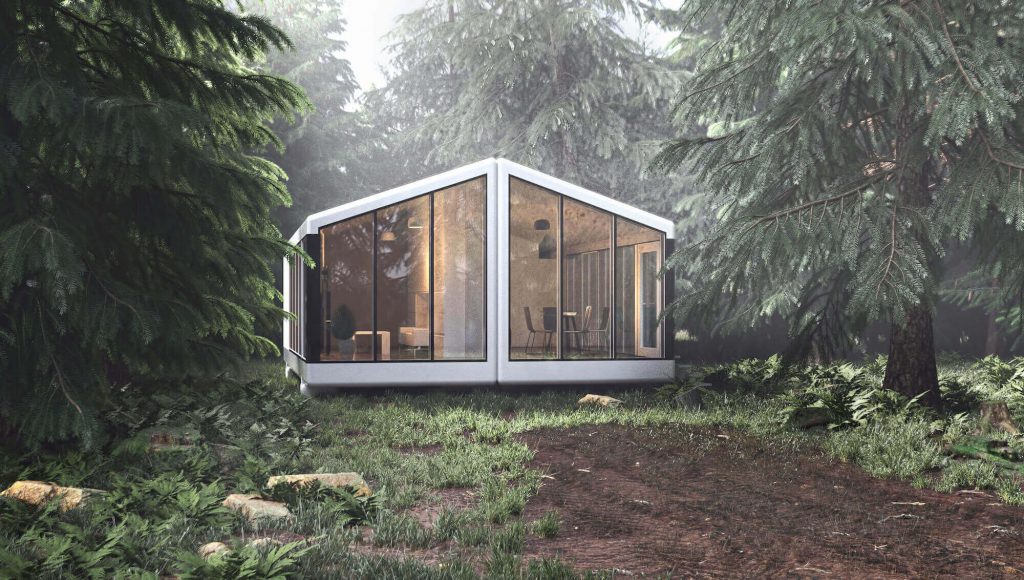
Others such as COBOD (www.cobod.com) provide construction 3D printing services, albeit in limited areas of Europe.
Another potential website to check out is www.weprinthouses.com. However, they are currently only taking requests and not orders. Additionally, at a cost of $100 per square foot for the construction alone, there is not much of a cost saving benefit transferred to the customers.
The company based out of Austin Texas has been awarded the first commercial permit to build a 3D printed house that can appraised and sold in the U.S. The construction project has been given the code name the Genesis. Construction begins February of 2020.
See our post, when will 3D printed houses finally become available where we look at the viability of 3D printed houses, plus when and where 3D printed houses will be commercially available to begin with.