3D printing is a manufacturing process used to make three dimensional objects by adding material layer by layer according to the computer-aided design model (CAD model).
In conventional machining, bits of material are removed from an oversized stock of material to form the required component. This process is known as subtractive manufacturing. Components are also produced through another process called casting, which is perhaps closer to 3D printing, where molten material are poured into the mold using different means such as pressure, hammers and dies.
3D printing differs from these methods as the process is often the inverse of the industrial manufacturing process used today and is consequently referred to as additive manufacturing.
Types of 3D printing technologies
Several techniques are used in 3D printing depending on the material needed and other factors. These techniques include, stereolithography (SLA), fuse deposition modeling (FDM), Digital light processing (DLP), selective laser sintering (SLS), electronic beam melting, selective laser melting (SLM), laminated object manufacturing (LOM), etc.
Difference between metal 3D printers and conventional 3D printer
In conventional 3D printing, plastic is melted and deposited layer by layer to form 3D product. The highest temperature for the toughest plastic is somewhere around 225°F (107°C).
On the other hand, it requires a blistering 2800°F (1537°C) to melt iron, the base metal in steel alloys. For some of the softer metals such as Tin, the melting temperature is 450°F (232°C). Since metals have too high melting points, the melt and extrude procedure is no longer economical to produce metal parts or metal 3D objects.
Due to the high melting temperatures required, metal 3D printer manufactures came up with several ways to engineer printers to overcome their shortcomings. Some of the approaches or methods developed for metal 3D printing include Binder jetting, direct metal laser sintering (DMLS), Directed energy deposition (DED), selective laser binding, etc. These techniques are used in metal 3D printers.
How metal 3D printing works
Metal 3D printing starts like all the other 3D printing techniques, where a 3D model is designed using computer-aided design software (CAD Software). By use of the computer-aided design software, the exact dimensions of the object to be printed are considered and simulation carried out to see the behavior of the object under several conditions.
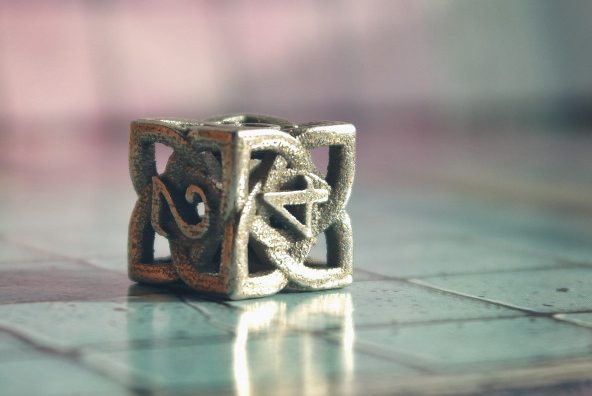
Before simulating, several parameters are keyed into the model. For example, material, force expected to act on the object, etc. After the CAD file development and simulation, the file is converted into a specific file format. The specific file format depends on the specific method being used for 3D printing.
After converting to a specific file format, the file is transferred to the printer by clicking the print command on the computer. Here, size as well as the orientation of the page, are selected depending on the type of 3D printing technique being used. The material to be used in the 3d printing is fed into the printer. After setting everything right, the printer starts to perform its function.
The following explains the techniques used in 3D metal printing.
Binder jet jetting
This technique of 3D printing is also known as inkjet 3D printing. The printing process starts like all the other 3D printing process as explained above. The 3D design and a slicer play a great role in the printing process. They tell the 3D printer’s onboard computer where and how to deposit the material.
After feeding the printer with metal powder and glue-like binding substance, the printing process is started by commanding print on the computer. The metal powder will be deposited in a thin layer and the binding material will be ejected from the 3D printer head, on top of each metal powder layer. The layer of the metal powder and binding substance fuse and begins to form the 3D object as defined by the 3D model from CAD. This process is repeated until the desired object is formed. Depending on the complexity and size of the product being printed, this process might take several hours to finish.
During the printing process, some powder remains around the design and is not fused, this acts as a support and should be separated from the object after the printing process is complete. After printing, the product obtained will be fragile and some air is contained in the object.
This process is faster compared to the other techniques of 3d printing, but the post-processing exercise may take a lot of time. To achieve better chemical as well as mechanical properties, post-processing (secondary processes) are required.
Examples of these secondary processes are sintering or infiltration. Sintering is where the printed part or object is placed in a very high-temperature furnace. In this furnace, the remaining binding substances are scorched out. In the same furnace, the remaining metal particles are bonded together which leads to low porosity in the part or object.
Infiltration involves placing the printed part or object in a furnace where the binding material is burned out and leaves void. Bronze is then used to fill the voids by capillary injection. This results in printed parts or objects with good strength and low porosity.
Advantages of Binder jet jetting
The advantages of using jet printing techniques for creating 3D metal products include:
- the metal binder jetting 3D printing process is a fast and cheaper process for 3D printing. It perfectly fits decorative objects, prototyping needs, ornamentals, as well as jewelry production.
- This application is advantages also because of its ability to create unique metal parts with good surface finish.
- The other advantage of binder jetting is that there are fewer restrictions on the geometry since no support is needed.
Disadvantages of Binder jet jetting
Disadvantages of binder jetting metal 3D printing are:
- The parts or the object undergoes time-consuming post-processing after printing (sintering process or infiltration process).
- Compared to bed fusion the products or parts manufactured have higher porosity.
- The other disadvantage is that the cost of material, as well as the printing machine, is high.
Direct metal laser sintering (DMLS)
This is also known as laser powder bed fusion (LPBF) or direct metal laser melting (DMLM) technology. This technology produces a 3D part using a 3D computer model. The working material used in a direct metal laser sintering printer is fine metal powder. For example, stainless steel powder, aluminum, and powdered titanium.
To create a 3D part using DMLS, a 3D model is prepared using CAD software. Then CAD model is converted to the specific file format, an acceptable format which can be fed to the 3D printer. Then the powdered metal is fed to the direct metal laser sintering (DMLS) 3D printer.
When the printing is initiated, a thin layer of the powdered metal is spread out by use of a roller. After this, the chamber of the printer is heated, but it doesn’t melt the metallic powder because the melting point is not reached. At this point, a laser is used to raise the temperature of the layer which is part of the design to a temperature just above the melting point. At that moment, one layer of the part is made.
The 3D printer spreads another layer of powder and the laser touches the correct spots for each layer to sinter the 3D object together. This process continues until the 3D project is created.
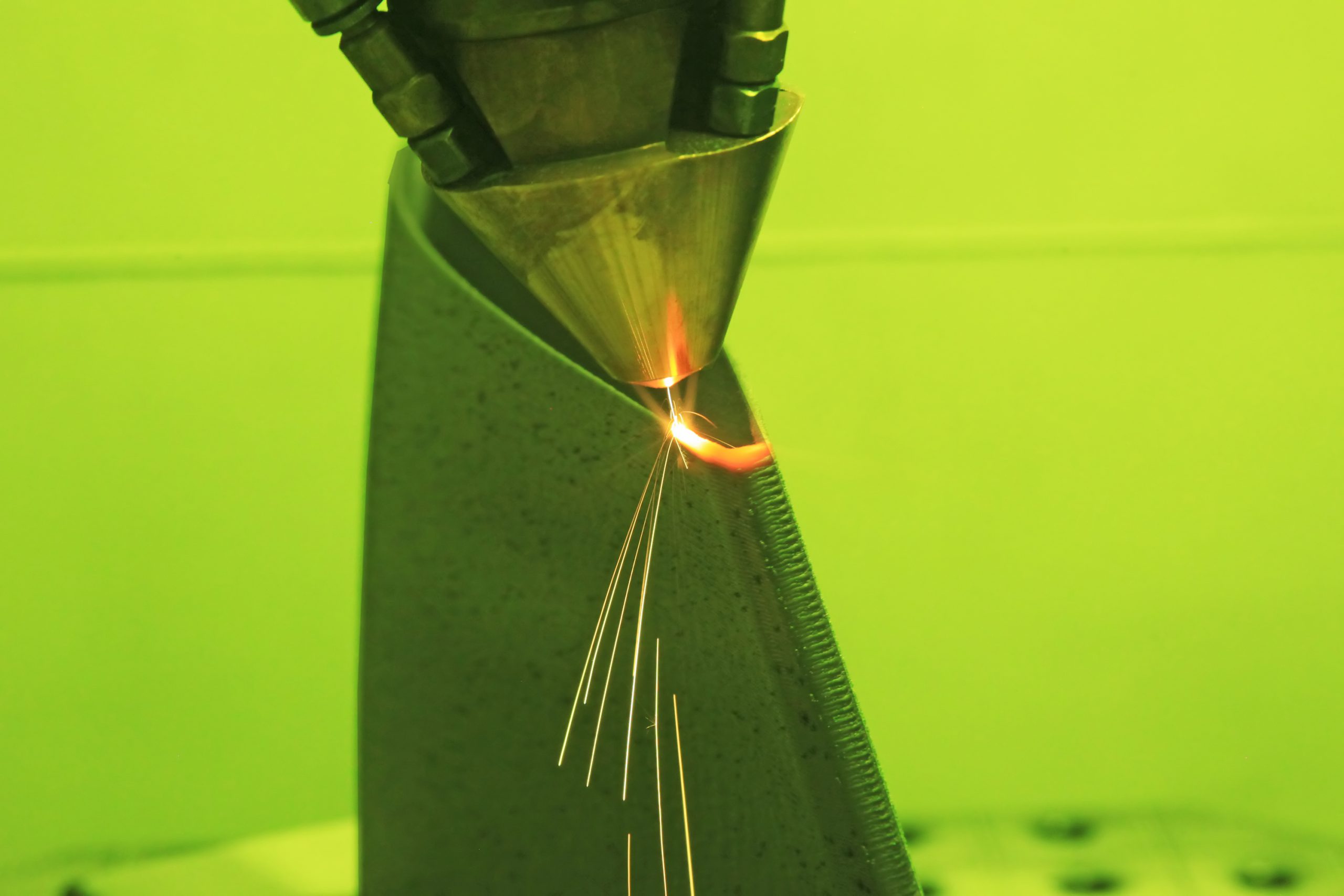
After printing the designed part or object, the printer, as well as the printed part or object, are allowed to cool down. After they cool down, the metallic product is lifted from the bed and the loose powered metal surrounding the part is removed.
Some of the model needs support structures to support it while the printing is taking place. In this case, after printing and allowing the printed part to cool, the support structures are removed manually from the part.
The last step in the printing process is post-processing. Post processing may be used to enhance the durability and strength of the produced part. The final metal 3D object created in direct metal laser sintering (DMLS) has comparatively high strength and lasts longer.
Direct energy deposition (DED)
In this technique, metallic parts or objects are created by melting the material and depositing them layer by layer on the workpiece. This technique can either use metal wire or powder material.
The Directed energy deposition (DED) 3D printer can apply plasma, electric arc, laser or electron beam to melt the metal wire or powder into a molten deposit.
This 3D printing technique is used for:
- low volume production,
- To repair broken parts
- Add features to already made part
- Produce simple parts
- Produce product prototypes
The steps followed to produce a 3D object or part using direct energy deposition as discussed below: The arm of the 3D printer is allowed to pivot around making it possible for the arm to reach all the points on the product being created as described by the 3D model produced using CAD software.
The metallic material which is provided is either in powder or wire form. The material is deposited from the printer nozzle. The material deposited on the object is heated to molten state using an electron beam, laser or plasma arc after deposition on the object. The above process is repeated. The materials are deposited layer by layer after which it solidifies to create a part or repair an existing object.
The advantages of metal 3d printing
The main advantage of metal 3D printing is the ability to produce parts and objects with complex shapes. Other advantages of metal 3D printing are as explained below:
- Compared to traditional methods of manufacturing, metal 3D printing is capable of producing complicated details faster. Metal 3D printing has opened limitless opportunities to companies as well as individuals by making it possible, less expensive as well as viable to for design which are complicated.
- This technology is able to produce objects with great precision.
- There is very little to no waste of material. Unlike traditional manufacturing methods, 3D printing techniques uses only the material needed to produce the part.
- The cost of production is less compared to other conventional methods of production. This is because of several reason which includes and not limited, to less wastage of material when this technology is used, the labor required to produce a complicated component or object is less and the production takes much less time compared to the other methods.
- For both high and low volume production, the cost per part remains the same for fabrication methods such as casting.
- Compared to conventional production process and techniques which require high storage for the raw material, machines as well as for storing finished products, metal 3D printing requires less storage. Products can be printed when needed which eliminated the need to produce excess products hence no storage is required.
- This is a modern environmentally friendly technology. Though a high amount of is power is used in 3D metal printing, little amount of pollutant is released to the environment making the processes arguably more environmentally friendly other means.
- 3D printing is flexible as a given 3D printer can produce any design that will fit within its build volume. For the traditional manufacturing process, they will require new tools, die, jig, etc. to create a new part when there is a change in part design.
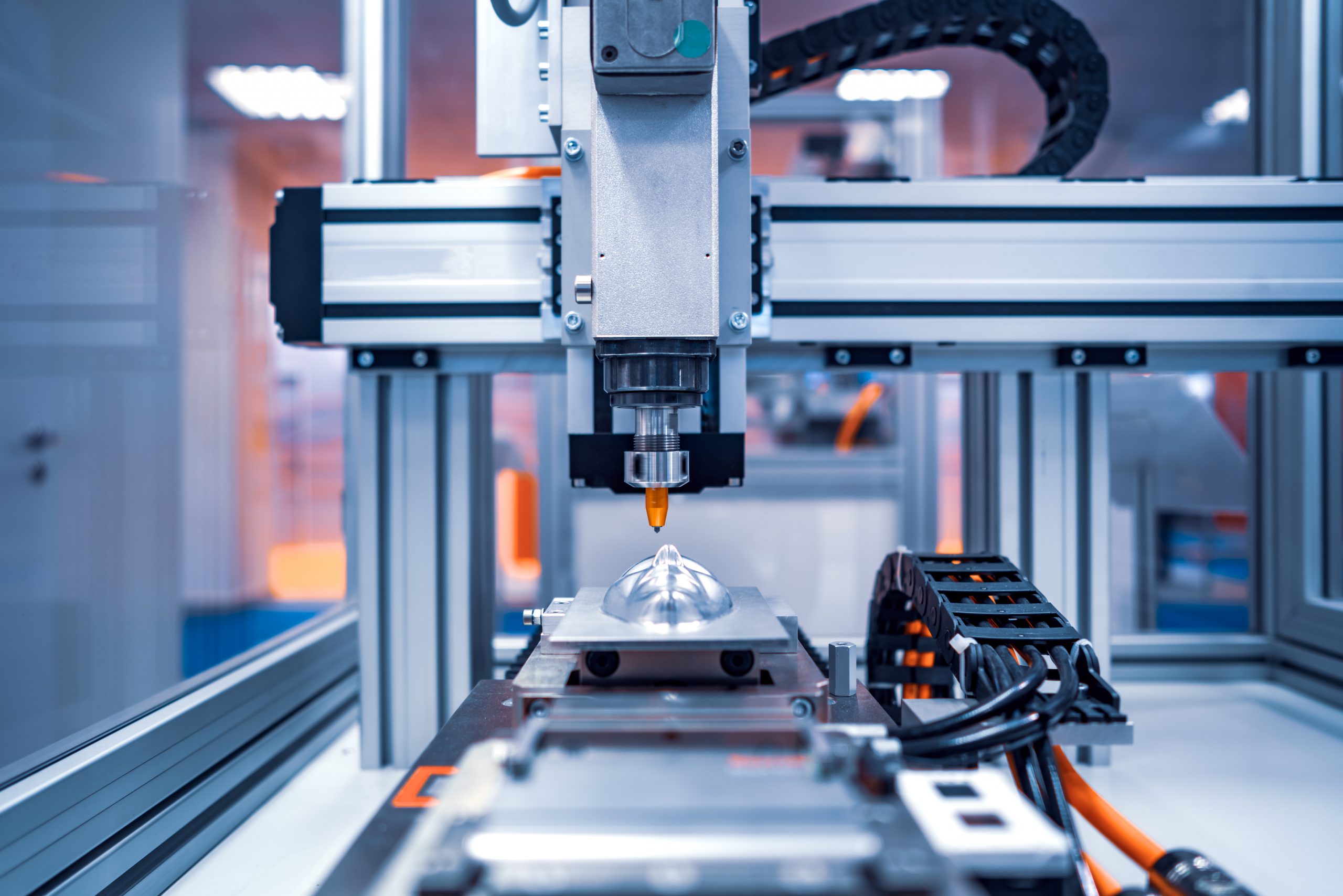
Some of the disadvantages of metal 3D printing include:
- The amount of money required to set 3D printing facility is very high
- Parts produce with current metal 3D printing technology tend to be inferior in quality (strength hardness, toughness etc.) compare to conventional means.
- High amount of energy is consumed
- People who were employed with production companies must acquire new skills when 3D printing is applied to produce the in production.
Conclusion
The introduction of 3D printing techniques in the manufacturing sector has opened limitless opportunities to companies as well as individuals by making it possible to produce parts economical as well as making it viable for design which were extremely expensive or complicated.
Though these 3D printing technologies has many advantages, they will not replace traditional manufacturing methods because of the disadvantages they have. We expect some of the factors which are limiting the use of 3D printing in many areas such as high cost of parts, and relative less/lack of accuracy on small scale to be resolved gradually as technology advances. We also expect the use of 3D printing techniques to increase as the technology advances.