Construction 3D printing has quietly positioned itself as the outstanding future of home building. 3D printed housing promises cheaper, yet just as durable and diversely designed housing options that can be built from the ground up in a matter of days instead of months. Well, that is the promise.
But one thing that many real estate investors along the general population is still in the dark about, is just when this technology – if ever – becomes available to everyday customers looking to construct or buy their dream homes.
In this article, we shall attempt to answer definitively this very question, and hopefully, provide a realistic timeline in the process as to when 3D printed houses as well as construction 3D printing in general, would become feasibly available to serve as practical alternatives to conventional housing and construction.
3D printed houses currently available for sale
Right now, practically, only haus.me is offering 3D printed houses that are for sale. But these are of the prefabricated variety.
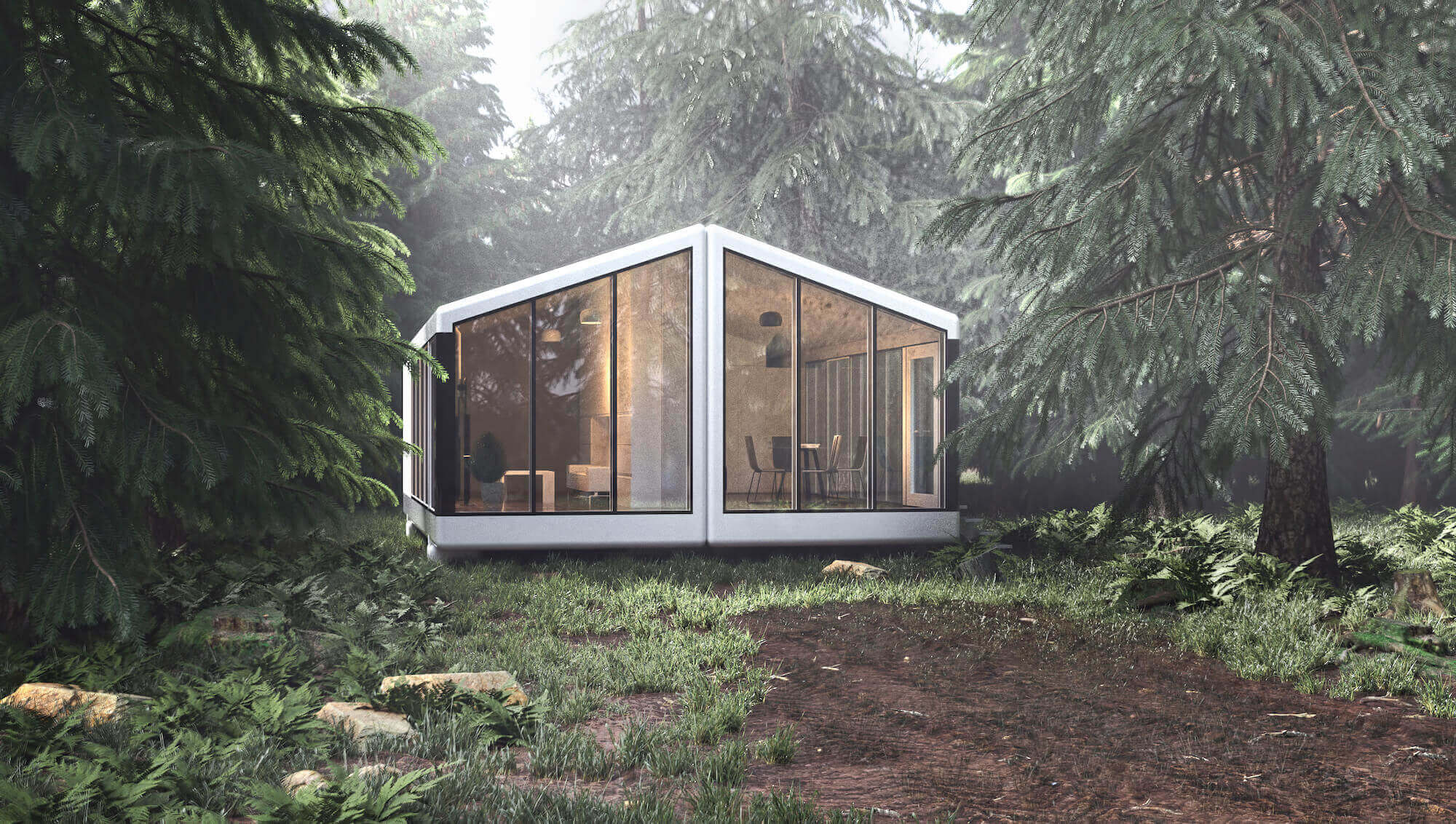
Almost all other 3D construction printer makers and construction 3D printing service providers tend to work with large-scale or high-profile projects where the municipality is either involved or was engaged for a long time in order to be granted construction permits.
The biggest roadblock, arguably, is government regulations regarding what can or cannot be allowed as a means of construction. Government regulations and construction permits vary wildly across the globe. But one thing they all have in common is the reluctance of public bodies to allow bleeding-edge technology to be used by the general population at such an early stage.
Timeline, location of availability and future expansion
Construction 3D printing is going to be used extensively in 2020 and beyond by governments, NGOs (Non-government organizations) and private corporations.
Update: Between late November and early December 2021, home builder SQ4D announced the listing of the first 3D printed family home on the open market via Zillow.com. The home located in Riverhead, NY, has 3-bedroom 2 baths and comes with a price tag just shy of 300k.
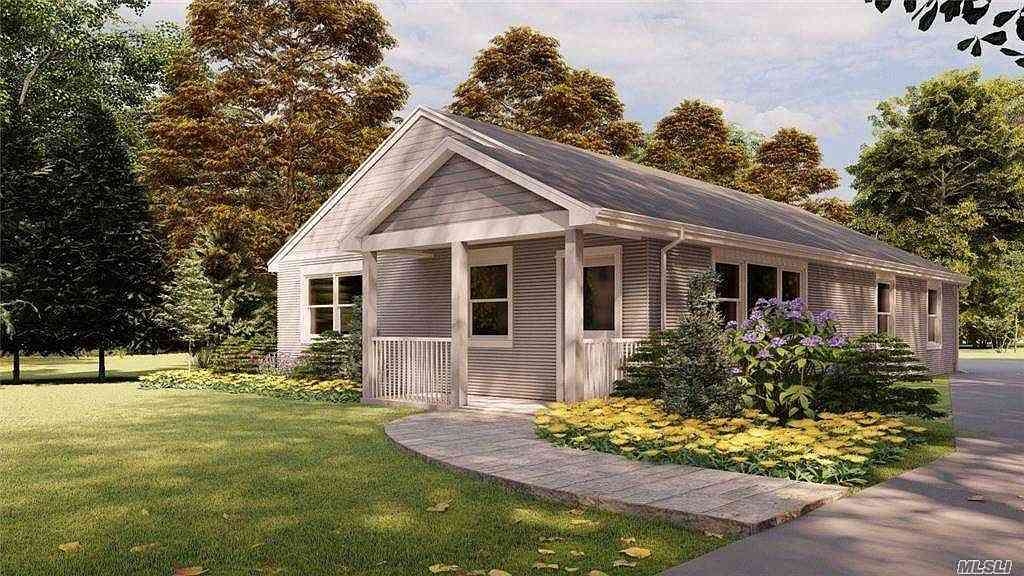
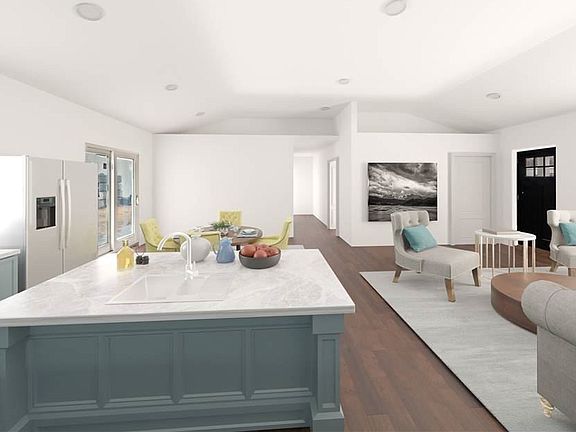
The reasons range from remaining leaders in cutting edge technology such as with Dubai’s commitment to have at least 25% of all new buildings constructed by 2025 and beyond to be 3D printed, to taking advantage of the shortened construction times such as with KSA’s commitment to create 1.5 million new private sector homes by 2030.
One thing that does not seem to be on-cards this year, however, is for construction 3D printing services to become available to the mass public. And while some pessimistic views hold that it may well be another decade before you and I can purchase our own 3D printed house or hire a construction 3D printing contractor the same way as a conventional construction contractor. However, based on prior and current projections, it is very possible that the development process will mature a lot sooner than later.
All major construction 3D printer vendors have already committed themselves to providing their construction 3D printing technology to a number of customers. This includes the likes of COBOD, ICON and many more.
In the United States, the first ever commercial permit to build a 3D printed house has been awarded to an Austin Texas based company and construction is set to begin on February 2020.
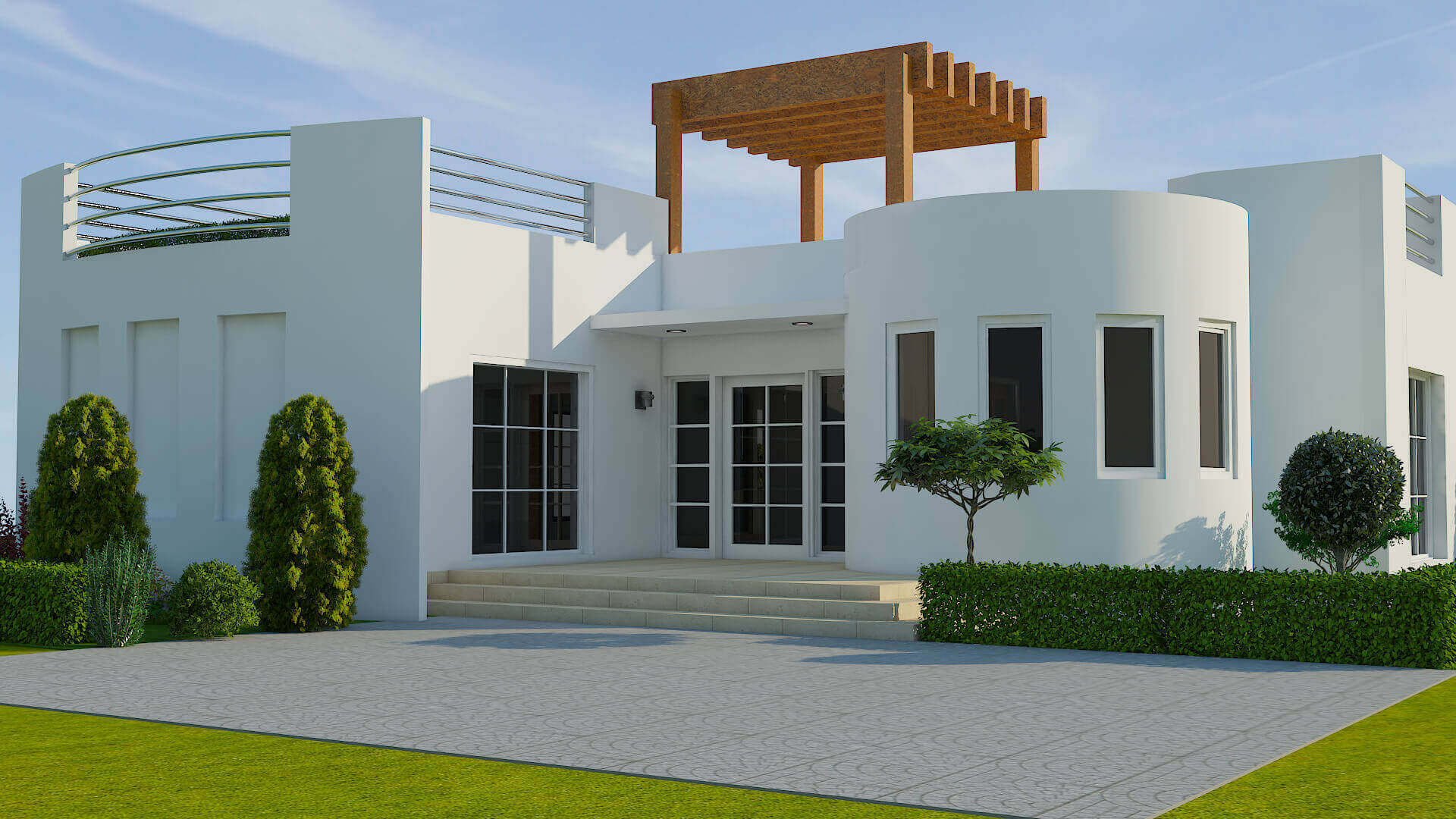
Another major contributory factor to believe in a quicker timescale would be the amount of consumer interest as well as the low entry barrier for new and existing engineering firms to adopt construction 3D printing technology as a means to tackle the sky-rocketing housing and construction costs.
Places such as India, Canada, the Middle East, China and many nations in Europe have start-ups springing up all the time who are making concrete 3D printing that much more viable while optimizing their bespoke hardware to work best with locally available materials.
The first for-sale 3D printed houses in Eindhoven this year are a testament to how quickly the industry wants to progress to a point where 3D printed houses are the norm and not the novelty.
In five to six years’ time, expect at least the developed world to offer ready-to-print housing services, or at the very least, much more easily procurable construction 3D printing services for the average home seeker.
Entry price of 3D printed houses
While it is safer to assume that the timeline for construction 3D printing to become much more viable and practical would be short. It would also equally be foolish to assume that the cost benefits would be transferred by all pioneering services onto the consumer.
Large sums of money are being spent in R&D for construction 3D printing every year. Once we reach a critical point where construction 3D printing is reliable, easy-to-use and cost-effective enough to be deployed at large-scale and on-demand, companies would rightly want to recoup at least a good part of their investments in the short-run.
Pricing of 3D printed houses is being targeted as costing half as much as conventionally constructed houses. However, a good rule for at least the first wave of available services is for it to cost around 70%-80% of conventional housing once you account for all additional costs – such as transportation of either the equipment itself, or the off-site 3D printed house modules. While these costs are incurred by the contractor, they will inevitably be transferred to consumers until competition pushes prices downward.
In some early cases, it may well cost more than conventional construction – such as with weprinthouses.com – for the novelty and innovation of the technology itself.
Over the long run however, we may see prices go down to somewhere around half of what conventional housing costs for small scale projects.
This is of course, excluding finishing costs, since those can be as extravagant or as low as one would want. But smartly designed 3D printed houses, should in theory, reduce finishing as well as long term maintenance costs.
See our complete guide, 3D printed houses – the definitive guide for an in depth look at 3D printed houses and the technology used to build them.
Evolution of construction 3D printing industry
Construction 3D printing is, in our times, a very real technology. Slowly but surely, construction 3D printing is leaving behind its “prototyping” phase and is being applied to real world applications where its advantages and promises have been highlighted in contrast to conventional construction.
We have come a long way from the automated brick-laying systems tested and experimented with more than 60 years ago.
Today’s 3D construction printers are capable, at least from a purely technological point of view, of 3D printing the entire concrete – or other suitable material – gray structure of the house in one go. Provided, of course, that the house or building being constructed via construction 3D printing fits within the “Printing Area” of the 3D printer.
And while we are not at the point where a single construction machine would be capable of 3D printing an entire house with all its amenities; such as electrical wiring, plumbing, decorations and so on. It does not in any way, take away from the fact that even simply being able to 3D print the gray structure (the walls) automatically via a construction 3D printer is a big step up from the technological constraints of conventional construction.
Notable examples of progress in construction 3D printing
Some notable examples of the progress of construction 3D printing technology – inching us ever closer to the future of 3D printing entire houses on our own – are:
Most recently, Apis Cor deployed their signature robotic-arm based construction 3D printer to 3D print the world’s largest 3D printed building ever – a 6900 square feet office for the Dubai Municipality which was finished – amazingly – after just two weeks of construction time.
The current focus of Apis Cor has now shifted much closer to home with the firm seeking to 3D print the first ever 3D printed house in Santa Barbara County, California.
COBOD’s clientele notably also includes the Kingdom of Saudi Arabia. To whom they have delivered their largest ever Gantry-style 3D construction printer that is capable of 3D printing 3 story tall buildings in one go.
ICON partnered with the non-profit New Story to 3D Print a whole community of some 50 3D printed houses in El Salvador, Mexico, demonstrating on-site the reliability and dependability of their approach.
Other noteworthy examples of the progress of construction 3D printing of course include the likes of Winsun and its Chinese competitors who have pioneered off-site 3D construction printing. As well as the likes of CyBe and Batiprint, whom are responsible for ongoing developments of construction 3D printing in Europe.
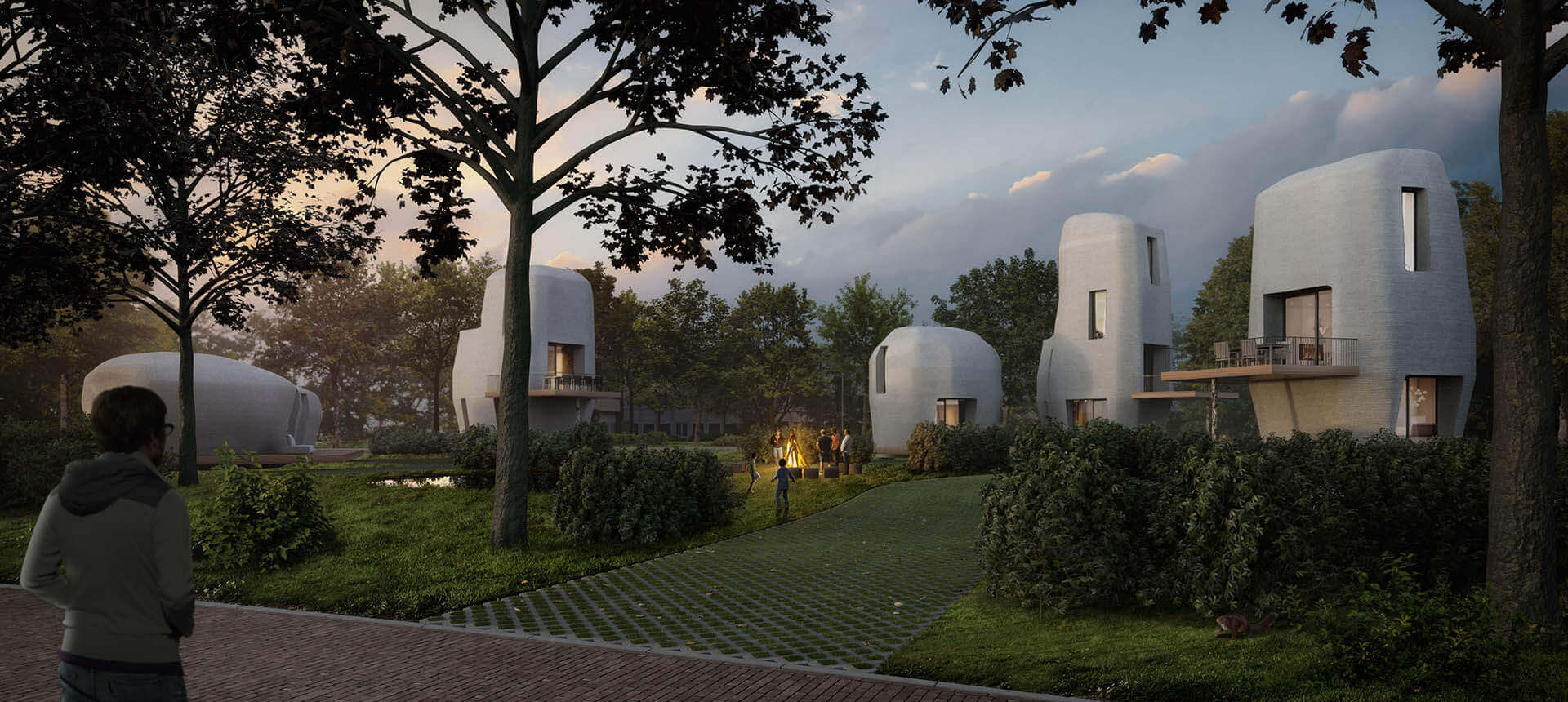
Impact of 3D printed houses on the construction and housing market
Dubai envisions a reduction of 90% in overall costs as well as a reduction of 80% in lead times for its various sectors. And that is with only 25% of all activities slated to involve 3D printing.
A similar story would be told across the globe. China recently completed the world’s largest 3D printed structure with Winsun finishing a revetment in the Suzhou area that is more than 500 meters long. The resultant revetment is just as strong, cost significantly less, and was able to follow the natural contours of the shoreline.
Lead times are cut down to days (or even singleday) from at least months or even years for large-scale projects. New building materials are being introduced. Material costs are reduced by a good chunk thanks to the lack of wastage, as well as precise layer-by-layer deposition of construction material.
Unskilled labor cost is mostly eliminated down to nil. While skilled labor is only required, at most, in a handful amount for small projects.
Make no mistake here: construction 3D printing, over the long run, will be nothing short of a revolution for both the construction and the housing industry on a global scale.
Things are changing fast in the world of construction 3D printing. And soon that change will be apparent for us to see and live in.
I am wondering who I can speak to about extending our kitchen using the 3D printed technology?
I am interested in having a 3D house built with geothermal for hearing & AC. A 3 bedroom 2 bath setup, in Central WA State. Any ideas of who can I contact and some designs of homes 🏡?