Man has always sought to make. We create, manufacture, build and alter at a baffling scale. We are obsessed and reverent towards exercising control on our surroundings. So much so, that it would not be an exaggeration to say that, as a collective, we value increasing and expending this control upon our environment, more than any other single endeavor taken up by humanity. This endeavor has been applied most notably through the furtherance of manufacturing technology.
3D Printing, has been arguably the most promising development in manufacturing since Henry Ford invent the assembly line. It has long been regarded to be the future of almost all types of manufacturing. In this piece, we will take a look at what 3D printers do in the real world and how they work. To begin with, we must first discuss where it all started.
Rapid prototyping and additive manufacturing
The earliest use-case and perhaps still the most widespread use today for 3D printers was their uncanny ability to print models out of a material, at a pace far greater than traditional methods available at the time. It was dubbed rapid prototyping at the time, a term that stuck with it to this day.
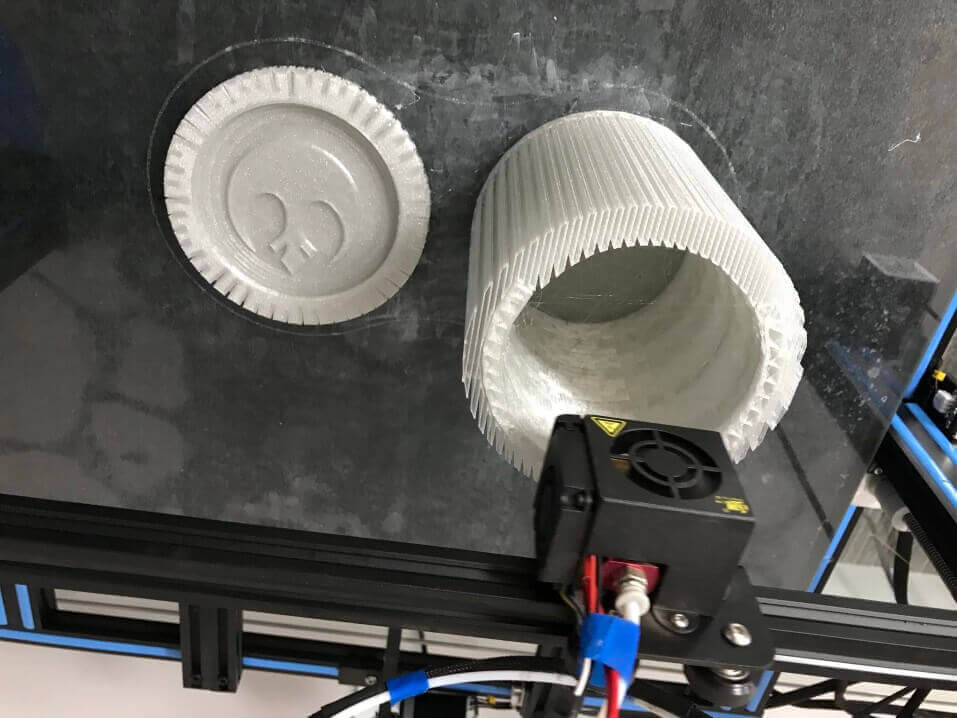
The efficiency of 3D Printing came from their ability to only used as much material as required to print a 3D model. It worked by adding material as needed.
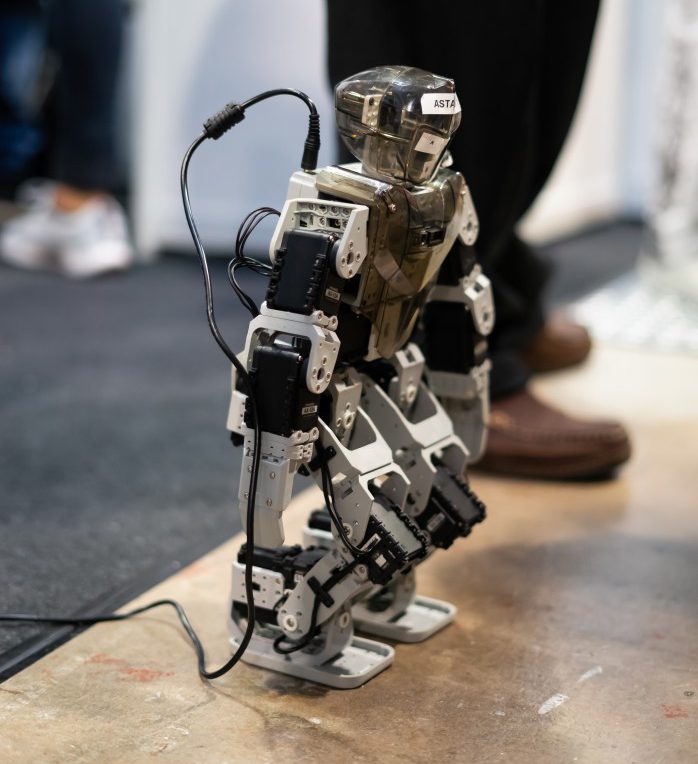
This was in stark contrast to the conventional approach of carving out or subtracting excess material from a block, to achieve the desired object.
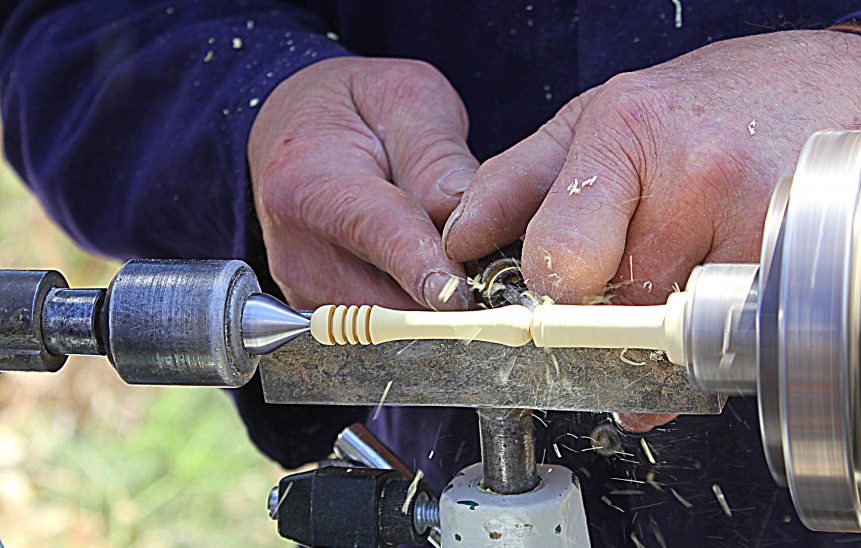
This is what came to be known and defined officially as additive manufacturing.
As with any emerging technology, early prototypes produced were expensive. They took a long time to be printed. In addition to that, they required constant monitoring by experts to ensure that bugs or kinks in the software and hardware stack did not ruin the resulting products. However, with time came progress in speed, cost, reliability and ease of use.
How 3D printers work
3D Printers work on the principle of additive manufacturing. That is, they can create objects by depositing and stacking layer upon layer of a material (or in their more advanced forms, many materials) to create a physical replica of a 3D model fed to it by a computer.
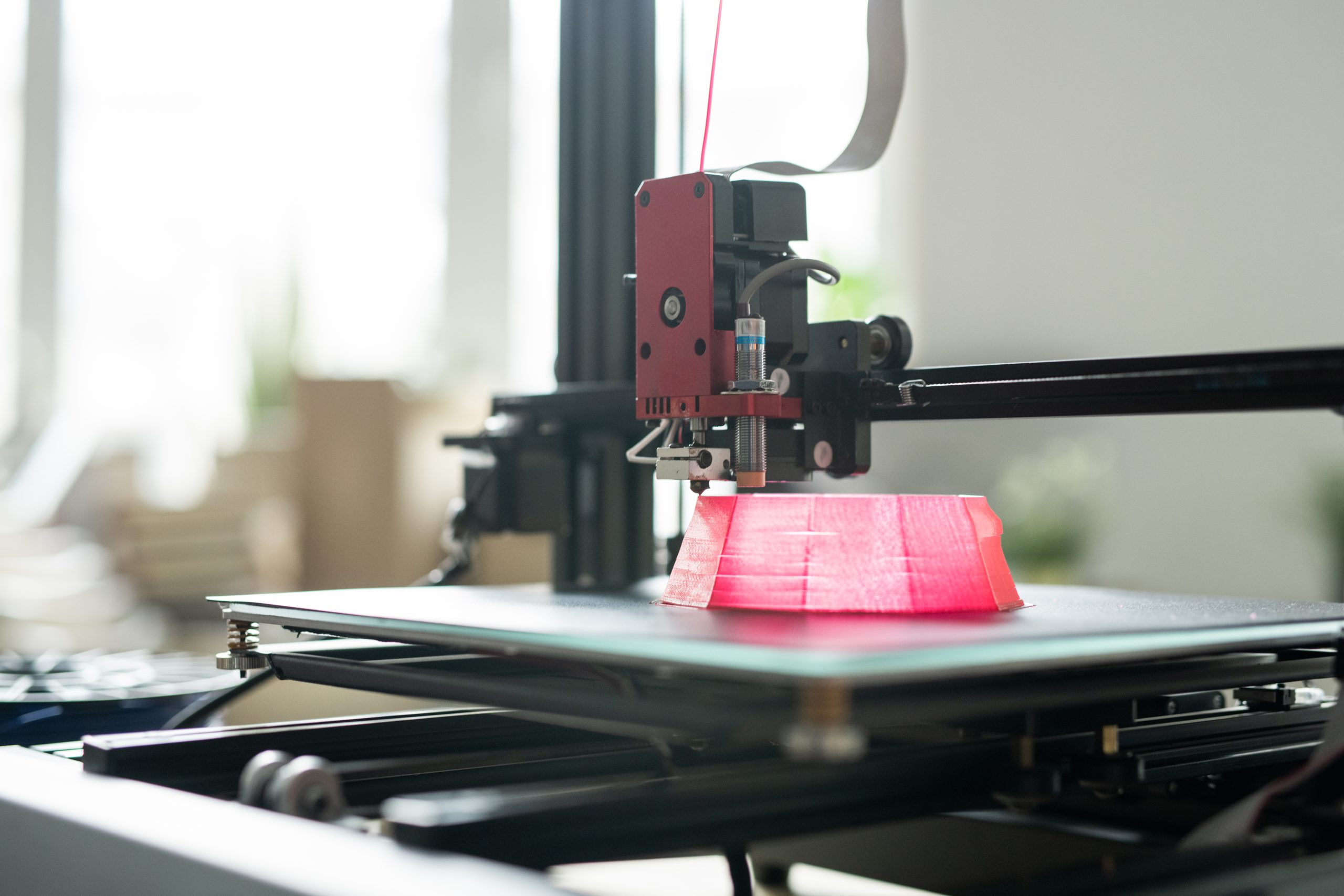
A 3D rendered model, in CAD or STL file format is converted using a converter software called a “slicer” that slices the 3D render data into layers. This resultant machine code data, called G-Code, is then read by the 3D printer as it prints the object. The process is similar to CNC machines, whereas CNC machine does the inverse of what a 3D printer does, it removes small pieces of material one layer at time from a big stock of material.
How different types of 3D printers work
The exact method for deposition and stacking, as well as what materials can or cannot be used differs bases on the type of printer and the 3D printing technology being used. While there are too many to count in this article, the most common types on the basis of material are discussed below:
1) VAT polymerization 3D printing
One of the oldest technologies for 3D printing, VAT polymerization works by printing 3D models out of a bed of liquid resin (photo-polymer), that is hardened by exposure to light.
Stereo Lithography, one such popular method, makes use of UV lasers guided precisely point by point with mirror galvanometers to enable high precision and accurate 3D Printing.
Another method employing VAT Polymerization, Digital Signal Processing is quite similar to SLA in that it also makes 3D prints via hardening/curing of photopolymers (polymers in this case typically refers to some form of plastic material). The primary difference is in the source of light. DLP utilizes a more traditional source of light instead of UV lasers, usually a blue laser. It exposes entire layers of photopolymer at one time. This type of broader exposure results in much higher speeds as compared to stereo lithography.
2) Extrusion based 3D printers (Fused Deposition Modeling)
Extrusion based 3D printers can be likened to computerized hot glue guns, in that they consist of a computer guided extrusion nozzle that deposits heated plastic filament in stacked layers on a printing bed.
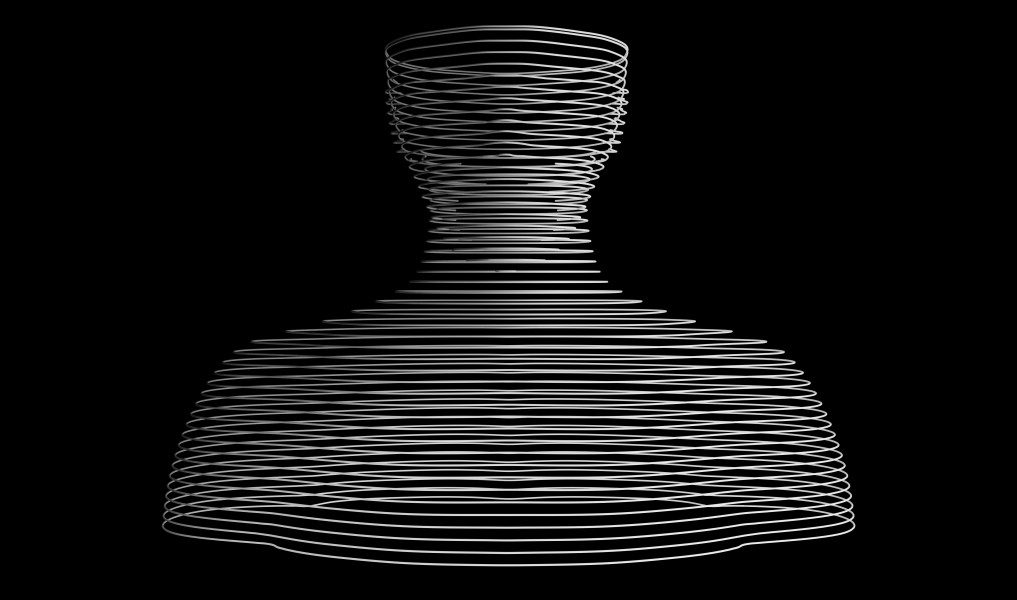
The most commonly used extrusion technology is Fused Deposition Modeling (FDM). Fused Deposition Modeling is also referred to as Fused Filament Fabrication (FFF). In FDM printers, filament is fed through a heating element and stacked in layers via an extrusion nozzle.
Filament is a term used to refer to the reels of material that the printer uses. Due to its simplicity and the use of plastics, FDM is by far the cheapest 3D printing technology.
3) Jetting 3D Printers
Jetting 3D Printers are similar in design to traditional inkjet printers, in that they deposit material on a printing bed by use of deposit-jet nozzles. This type of design makes Jetting 3D Printers some of the fastest and most accurate printers available.
In Material Jetting 3D Printers, the printing bed is lowered after deposition. Curing and hardening of the deposited photopolymers takes place via UV light exposure within the printing chamber.
In Binder Jetting 3D Printers, a thin layer of powder material kept in a chamber either above or on the sides of the printing bed is deposited on the printing bed and is smoothed by a roller/scraper. The binder droplets are sprayed onto the previously rolled material and cured before the next layer of powder is deposited and the process is repeated for all the layers.
Unlike Material Jetting Printers, Binder Jetting Printers can be used with metallic powder or even sand or silica powder (an oxide of silicon).
4) Selective Laser 3D Printing
Selective Laser 3D Printers use lasers to sinter, to adhere without fully melting, powdered material (either plastic or metal) placed upon the printing bed (similar to binder jetting 3D printers) in a layer by layer fashion.
Alternatively, higher intensity lasers or electron beams can be used with metal powders to melt metal powders into place.
Owing to the maturity of this process, selective laser 3D Printers are the most popular choice for printing metal parts.
What 3D Printers Do
3D printers are still regarded as being somewhere between a hobbyist’s neat kit, to the manufacturing industry’s next big thing. However, the reality is honestly a lot more grounded than the sci-fi inspired depictions that 3D printing garnered over the years.
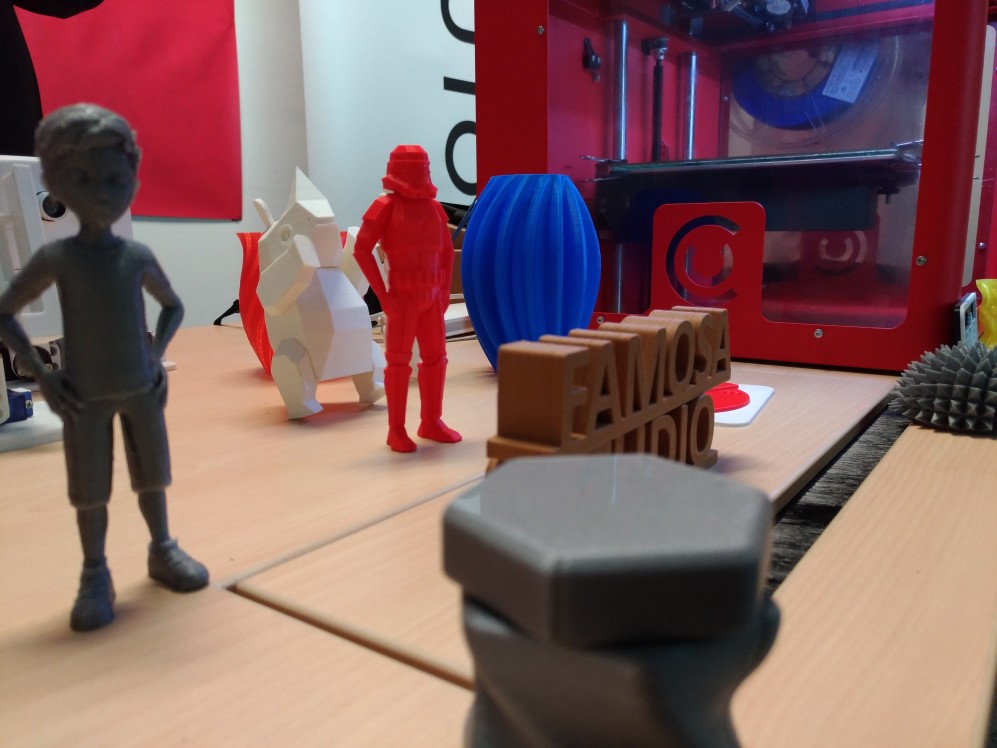
The beauty of 3D Printing technology lies in its flexibility, cost reduction and wide possibility of use-cases. Much more than just a hobbyist’s sidekick to craft custom figurines and thingamajig, 3D printers are being utilized every day to accomplish manufacturing tasks that may have otherwise taken much more time as well as money.
Prototyping
FDM 3D printers continue to play a huge role in prototyping, with automotive industries utilizing their speed and low costs for even full-scale prototyping, with custom built, room sized 3D printers. Fit prototyping in general, has seen the cost and speed gains by moving to 3D printers. Fit prototyping is the process where prototypes are built to exact size, fitted into an engine for example before molding of a finished piece has even began.
Industrial Applications
Below are some examples of how 3D printers are being used in an industrial setting to assist in the manufacturing process.
Machine parts and tools
Metal 3D printers are now used by large scale engineering companies to provide on-site custom designed 3D parts to their clients. Those companies are able to tailor every 3D print to exact customer needs, at a fraction of the cost. Similarly, tools and other such items can be easily 3D printed to specification. This allows for greater customization, and thereby benefiting companies in keeping costs down.
Stratasys, one of the oldest 3D printer makers in the industry, has designed entire 3D Printing Rooms with lines of 3D printers mass printing industrial parts at a fraction of the cost and time of traditional manufacturing.
Airline Industry
The Airline industry was one of the early adopters of 3D printing. Metal 3D printing has allowed these companies to replace big, simple but heavy support structure pieces, with equally strong complexly engineered lightweight substitutes.
Further, more traditional FDM 3D Printing is also utilized in upgrading airplane cabins to spec. via retrofitting.
Medical Applications
The endless design possibilities enabled by 3D printers, has allowed the medical industry to provide tailor made high quality prosthetics and implants to patients who would otherwise may have had to either settle for something lower quality, or pay through the nose and wait much longer to have their needs met.
Niche Usages
Perhaps the more mainstream uses of 3D printing, these are the more specialized application of 3D printing technology.
Food
Indeed, you have read that correctly. Based on the extrusion design, 3D food printers have become a niche attraction at high-end fine dining restaurants. Moreover, startups have used this flexible approach to create unique high-quality processed food from food scraps that would have been otherwise wasted.
3D Printing has also been looked at as a viable possibility to produce high quality vegan meat, with its layer by layer precision allowing for much greater texture control.
Fashion
As with all new technologies, designers and fashion gurus around the world have begun developing and experimenting with 3D printed fabrics made from soft wearable materials. Often times utilizing multiple materials to produce both high aesthetic and wearable quality.
Some specialized startups have even made a business out of making and selling 3D printed jewelry, gear and clothing.
Housing
Perhaps the brightest promise of 3D printing. The house building industry is finally realizing the potential of 3D printing to produce low-cost housing by custom built concrete extrusion 3D printers capable of printing complete houses in 1 or 2 days.
And the cost? Less than $5000 for a 650 square foot single bedroom house.
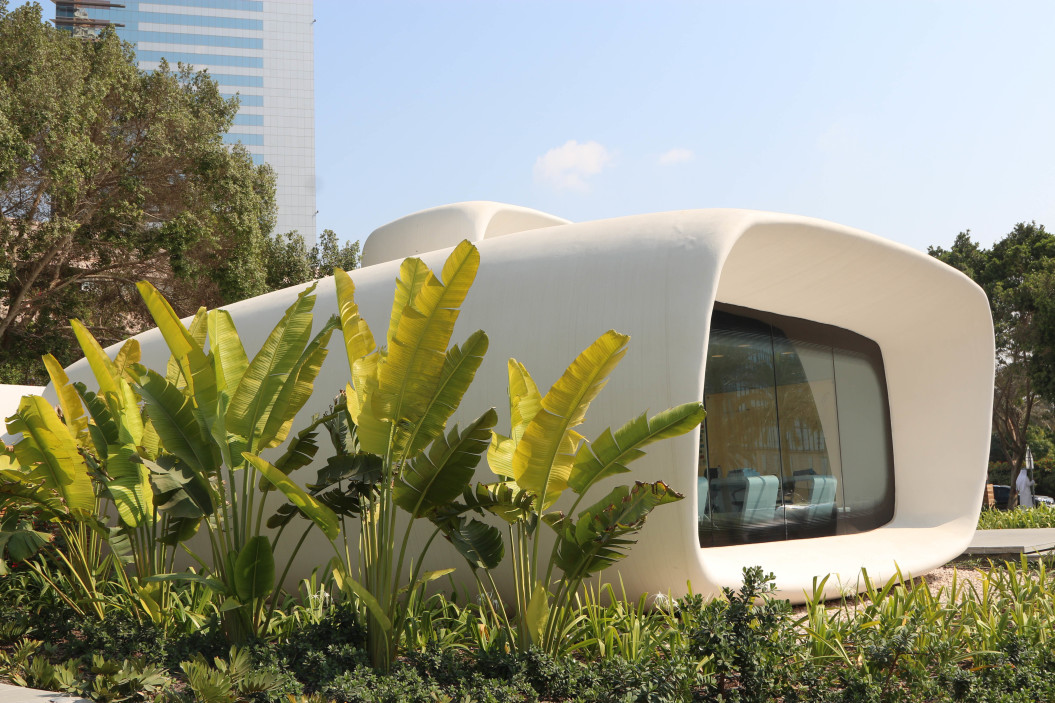
The future of 3D printing
3D printers are, despite all of their progress, still very much a developing technology. A good 3D printer back in 2014 cost upwards of $2,000. This year many options are available even for less than $500.
This boom in 3D printers doesn’t look to be slowing down anytime soon. With time it may very well be possible that all of us own a 3D printer and printing out our own phone cases, or toys, or even furniture may become as second-nature as heating food up in a microwave oven.
One thing is for sure, however, 3D printing is here to stay, and while it may be premature to say that it has filled all its promises, it most assuredly, is making steady progress.